With increased interconnectivity in the global market, safe product packaging throughout the supply chain becomes paramount. Products must endure transportation, handling, and storage to ensure that they reach their destination without defects. It is at this point that drop testing becomes an increasingly important quality assurance process in packaging and logistics.
We'll cover the value of drop testing, the drop tester machine, and the ROI of integrating such technology in testing labs. We'll also discuss the various models and specs and how they relate to international test standards.
Let's get in!
Why Drop Testing Matters for Packaging and Logistics
Normally, drop testing simulates the impact a package may bear during transit and delivery, making sure that what's inside isn't affected by handling, rough roads, or accidental drops. It is an evaluation of packaging strength and resistance, thereby representing one of the best ways to prevent product damage and, consequently, customer dissatisfaction.
Each year, billions of products wind their way around the world, and millions of these are probably damaged on their way. Studies show that a large proportion of product damage is caused by mishandling in shipping, often involving drops from different heights and angles.
A drop tester machine simulates and recreates the exact real-world condition of dropping a package from specific heights and onto predetermined surfaces. It works towards the evaluation of durability in the materials used in packaging and the product inside under severe controlled conditions. By simulating these conditions, manufacturers and suppliers can use this information better when it comes to packaging design, thereby protecting products more and preventing losses due to shipping damage.
Test cycles and procedures are the backbone of drop testing.
To carry out the complete test, several cycles are run on each package under test. Here are the three most widely used drop test procedures:
Twenty-Six Drop Cycle (Boxes): Each of the six faces (front, back, left, right, top, and bottom) and all of its twelve edges and eight corners is impacted by the test package as it is dropped onto. In this exhaustive test, all the orientations in which a package may experience shipment are replicated.
Corner Drop Cycle (Boxes): In this test, the package is dropped on all of its eight corners. Being the first points of impact often makes corner points, testing them would ensure that the packaging can handle possible impacts to its weakest points.
Dropping any package twelve times on all its twelve edges is the goal of this process set of conditions in which the most common modes of failure very often occur during transport. Manufacturers can make packaging stronger and more robust by evaluating the strength of the edges.
Benefits of Adding a Drop tester in your lab;
A drop tester can provide excellent returns on investment for a company that is looking to make improvements in packaging quality and reduce costly product damage during transport. Here's how:
Reduced Product Damage: Damaged product costs are at an approximate level of $300-$500, notwithstanding shipping costs or loss of customer loyalty; hence, preventing this damage through superior packaging saves tens of thousands of dollars every year.
Improved Packaging Design: Early weakness in the packages means that a manufacturer can enhance the product at an early stage, thereby reducing the chances of redesigning with cost when the designs are finalized. Such a proactive approach improves times by up to 30% for packaging design and prototyping.
Enhanced Brand Image: Customers tend to return broken products to the company in greater numbers, thus increasing return rates and reducing customer satisfaction. A more robust packaging solution can increase the rates of customer retention by 10-20%.
Conformity with Specifications: Certain industries are heavily regulated in terms of packaging standards (ASTM, ISTA, ISO). With a drop tester machine, the company is guaranteed to be in line with these standards; thus, saving the company from fines and possible legal liabilities.
Increased Time-to-Market: A drop tester accelerates the validation of packages, therefore putting products on the market quicker than anyone else who isn't using it; thus a developer can be in and stay competitive in the marketplace.
Deep Dive into our Drop Testers:
We as a leading drop tester manufacturer provide you with a range of models of drop tester machines, from small parcels to big heavy-duty shipping containers. Our machines comply with critical standards, such as ASTM D5276 (Standard Test Method for Drop Test of Loaded Containers by Free Fall) and ISTA 1A (International Safe Transit Association).
Some of our top models are:
1. Drop Tester (PDT - 0134)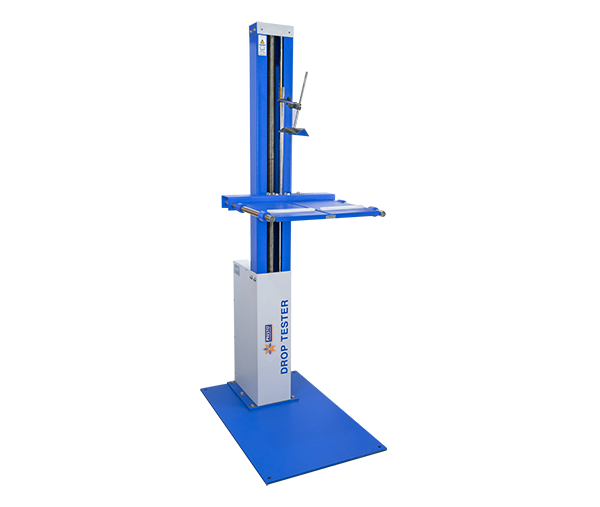
Standards:
IS: 7028 Part IV
Types of Tests it can perform:
-
Straight Drop
-
Angular Drop
-
Safety: Locking pin
Technical Specifications:
-
The height of the laboratory equipment is 1.8 meters (Adjustable).
-
Higher-height models are also available.
-
Load can be exerted up to 50 kg.
-
The maximum and Minimum height of the drop are 1800 mm and 750 mm respectively.
-
Sample Mounting table –465 * 445 mm
-
An adjustable angle holder is provided with the device.
2. Drop Tester Motorized Pneumatic ( PDT - 0135)
Technical specifications:
-
Testing drop height – Min – 380mm, Max – 1800mm
-
Maximum weight of the test box – Up to 60kg
-
Motorised lift speed – 100 mm/minute
-
Power – 220V AC, 5 Amp, Single phase, 50Hz
-
Opening Actuation – Pneumatic cylinder
-
Least count – 1mm
-
Maximum dimensions of the test box – L 500 X W 500 X H 500mm
-
Dimension of the floor – 1200 X 900 mm
-
Compressed air required – Filtered, regulated 5 bar, 5 cfm of airflow
FAQs
What Does a Drop Tester Do?
A drop tester is a simulator that mimics the shock a package could encounter during shipment. It drops a test package from a known height onto a surface to evaluate the strength of the packaging and the item contained.
What is the Application of a Drop Tester?
Drop testers are used to test packaging material effectiveness in providing content protection against damage in the shipping process. It also contributes to manufacturers and transportation firms developing better designs of packaging to minimize loss or product damage before they reach their destination.
What does it test for?
It determines the strength and durability of the packaging against impacts, drops, and shocks it may suffer at any given time during handling, shipping, and delivery. This tests the capability of cardboard, plastic, and foam-based packaging material.
Enhance Your Testing With Our Drop Testers
A drop tester machine introduced to your lab will revolutionize your packaging processes saving you money, time, and resources in the long run. It will ensure that your products are protected during shipping, customer satisfaction is improved, product damage is minimized, and you are a step ahead of the regulatory standards.
We offer high-quality long-lasting drop testers for almost any testing requirement. From small packages to heavyweight items, we have a solution for you.
Want to learn more? Contact us today for a consultation or to request a quote for a drop tester price tailored just for your specific needs!
Phone: +91-9210 903 903
Mail: info@prestogroup.com